Tsinghua University, China
In the late 1920s, E.S. Davenport and Edgar Baine, two researchers at the United States Steel Corporation Laboratory in the state of New Jersey, the United States of America (USA), were undergoing pioneering metallurgical studies, specifically focusing on developing new forms of steel. Their work culminated in the development of a new form of steel – bainite steel – which has exceedingly high levels of hardenability (the capability of a metal to be hardened by heat treatment), toughness and tensile strength. In the 1950s, the development of air-cooled (cooling through exposure to air) bainite steel using molybdenum (Mo), a chemical element found naturally in certain minerals throughout the world, was a significant breakthrough and took bainite steel from the laboratory to the factory.
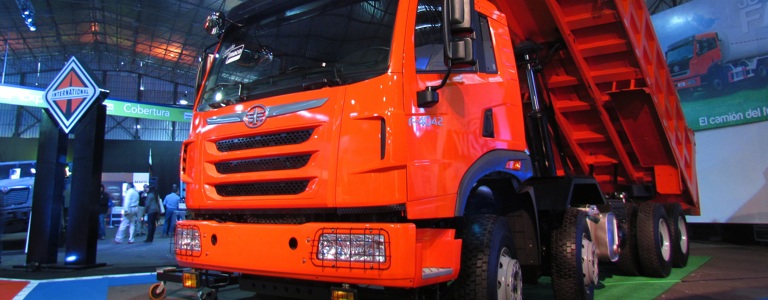
Air-cooled bainite steel quickly became highly desirable because of its unique properties, and became one of the most sought after steels for use in a variety of applications, from automobile parts to construction machinery. However, it remained exceedingly expensive due to the high cost of Mo and the technology and equipment necessary for isothermal treatment (heating a material at a constant temperature), both of which are required for bainite steel. As a result, air-cooled bainite steel was out of reach for many emerging economies. However, in the late 1970s, three professors – H.S. Fang, Y.K. Zheng and B.Z. Bai – from Tsinghua University (TU) in Beijing, the People’s Republic of China (China), made a breakthrough in air-cooled bainite steel that would make it more cost-effective while retaining its desirable properties.
Research and development
To produce steel, iron alloy is heated and goes through different phases during the process. These phases are called microstructures, and each has different properties. By using isothermal treatment, iron alloy can be heated at the level of a desired microstructure and then cooled, which transforms it into a variety of steel which retains the properties of the specific microstructure. Davenport and Baine’s research and development (R&D) was focused specifically on the isothermal transformation of austenite, the first microstructure after ferrite (the metallurgical term for solid iron alloy). During their R&D, they discovered that when austenite was isothermally treated at temperatures between 250°C – 550°C, a previously unknown microstructure forms.
The new microstructure that Davenport and Baine discovered was unlike anything they had ever seen, and in 1934 it was officially named bainite in honor of Mr. Baine, who pioneered the research. Early efforts at using bainite steel were limited because of the then complicated process of isothermal treatment, but the development of Mo bainite steel in the 1950s was a significant breakthrough. Even so, it remained an expensive and difficult form of steel to produce. As news of the discovery of bainite spread, researchers around the world started to investigate applications and other production methods for the new microstructure.
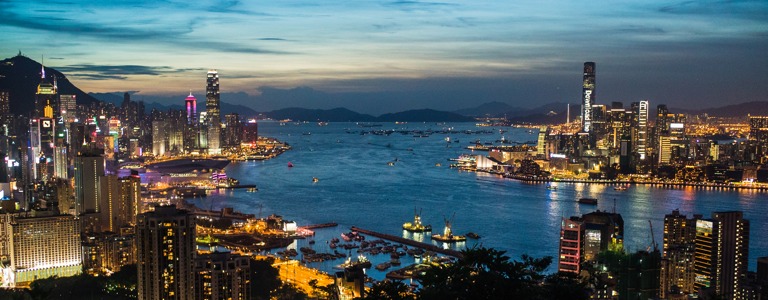
At TU in Beijing, Dr. Fang and his research team was one such group, and they knew that the largest obstacle to air-cooled bainite production was the use of expensive Mo in the isothermal treatment process. With a US $2,000 grant from the University, the team accordingly undertook experiments using different chemical elements to find a more cost effective method. One of the substitutions for Mo the team used was manganese (Mn), a cheaper chemical element that is found naturally in many minerals in the Earth. When Mn was used in the isothermal treatment process, Dr. Fang discovered that it can change the shape of the temperature time transformation curve (the TTT curve). The TTT curve is an isothermal transformation diagram which shows the relationship between temperature and the time taken for the decomposition of austenite into another microstructure when the transformation occurs at a constant temperature. The plotted curve shows the required isothermal treatment times for various microstructures to occur.
When Dr. Fang’s research team used Mn, they noticed that the curve was redistributed and affected the solute drag effect in a unique way. The solute drag effect is a phenomenon in steel development that markedly slows or stops ferrite growth when sufficient concentrations of carbon and an effective solute are present, the reaction temperature is relatively low and ferrite boundaries have migrated far enough to pick up the dragging solute. When Mn is used, a bay-like shape in the TTT curve is formed at around 600°C, which enhances the solute drag effect and thus further restrains ferrite growth and refines the resulting bainite. Through these results the team discovered that Mn-series bainite brings about the same results as Mo-based bainite.
With this discovery, the researchers proved wrong the traditionally held belief that air-cooled bainite can only be obtained by using expensive Mo. Moreover, Mn-series bainite has many advantages over Mo-based bainite, which include a higher hardenability, an excellent balance of strength and toughness, a simple alloying process (the combining of one metal with other metals), and reduced costs in both raw materials and production.
Invention
Since the early 1980s, Dr. Fang and his team used their discovery to invent different types of Mn-series air-cooled bainite steels with low, medium and medium-high levels of carbon. One form in particular was the early breakthrough of Mn-series low carbon granular bainite steel, which proved for the first time that an optimal combination of strength and toughness can be achieved in bainite steel by controlling the size, quantity and distribution of the martensite/austenite (M/A) islands (particles of the martensite and austenite microstructures that remain in the steel). The Mn-series air cooled bainite steels developed at TU each have different properties and are suitable for a variety of applications. The success of the invention led to the State Education Commission (later renamed the Ministry of Education) authorizing Dr. Fang and his research team to form the Bainite Research and Development Center (BRDC) at TU in 1990.
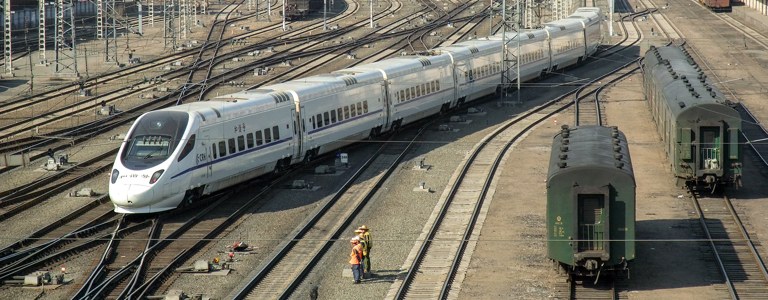
In 2009, Dr. Fang and his team invented Mn quenching (rapid cooling with a liquid such as oil or water) bainite steel, the second generation of Mn-series bainite steel. This advanced type of Mn bainite steel can meet the performance requirements of most steels used in a variety of industries, reduce the necessary amount of alloying content, increase the hardening capability and improve welding ability.
Partnerships
At the time Mn-series bainite steel was developed, because there was no official intellectual property (IP) or technology transfer system in place at TU, partnerships were used as a vehicle to stimulate interest and promote commercialization. The Research and Development Management Department (RDMD) of the University was formed in 1983 and handled all such partnerships and resulting technology transfer issues. In order to facilitate the commercialization of technology developed at TU, shortly after its creation RDMD entered into a cooperative agreement with Yunnan province in southwestern China. The core mission of this agreement is to realize science and technology development of companies, universities and government enterprises in Yunnan through assistance from TU. To realize this, Yunnan province established the Yunnan-Tsinghua Science and Technology Cooperation Office and the Yunnan-Tsinghua Science and Technology Cooperation Fund.
In March 1998, the agreement resulted in the successful transfer of Mn-series bainite steel technology to Gejiu Metallurgy and Mining Machinery Corporation (Gejiu) through the signing of a Memorandum of Understanding (MOU) with BRDC. Because TU and BRDC are government-funded institutions, such MOUs are necessary for submission to the local government, which then approves the partnership and technology transfer and provides other assistance. In the case of this agreement, the government used the Yunnan Economic and Trade Commission and the Science and Technology Commission to help facilitate the partnership. A mere month later, the partnership was approved through the signing of a tripartite contract between BRDC, the Yunnan-Tsinghua Science and Technology Cooperation Office, and Gejiu. BRDC provided its know-how and assisted Gejiu in implementing the technology to produce Mn-series bainite wear-resistant steel balls and steel castings, and also provided technology and assistance to improve the company’s R&D capacity, increase production and promote further potential commercial development of Mn-series bainite steel products.
Another important milestone came in 2000, when the Jinan Iron and Steel Group Corporation (Jinan) in the eastern province of Shandong developed a breakthrough in steel production. Jinan is a large manufacturer in the region of high strength steel plates, and prior to receiving Mn-series bainite technology from BRDC, it reached its performance capacity with the traditional technology that was at its disposal. The company was producing plain carbon steel with a tensile strength of approximately 300-400 MPa (megapascals, a measurement of stiffness and tensile strength). Jinan entered into an agreement with BRDC that was similar to that of Gejiu, and BRDC provided the Mn-series bainite technology and know-how to the company. With the introduction of this technology, Jinan was able to produce hot rolling low carbon Mn-series bainite steel plates that can achieve a tensile strength of 700-800 MPa. Called JB785, the new product maintained a high level of performance and strength while remaining cost effective. By 2011, Jinan perfected its application of the technology to produce Mn-bainite steel plates which can sustain pressure of up to 800 MPa and therefore yield even higher levels of tensile strength.
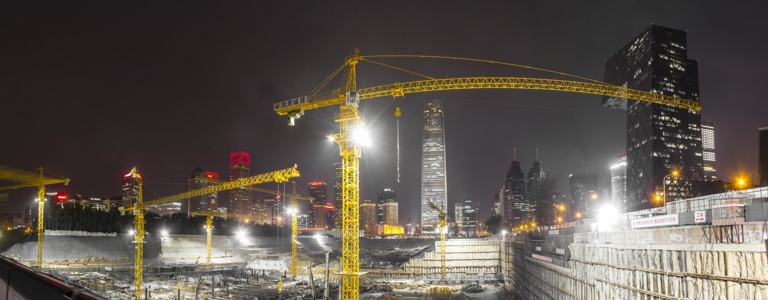
Patents
With the creation of the Tsinghua Patent Agency (TPA) of TU in 1984 and the enactment of the Patent Law in China that same year, the University made its first domestic patent application in April 1985, which was for low carbon Mn-series air-cooled granular bainite steel (#85100080). An application for medium carbon air-cooled Mn-bainite steel followed in April 1986 (#86103008), and the University went on to make nine more national patent applications for Mn-bainite related steel technologies. In 2003, TU made a patent application for its related Mn-Si-Cr (manganese, silicate, and chromium) air-cooled granular bainite/ferrite polyphase steel. The patent was granted in China in 2005. In 2008, TU made its first patent application for its Mn-series water-quenching (rapid cooling with water) bainite steel (#200810223422.X), and followed this up in 2009 with an application for Mn-series quenching bainite steel (#200910093285.7). This was followed up with a patent registration for a preparation method for air-cooled bainite steel that was granted in China in 2011.
Eager to take advantage of the IP system to commercialize its products abroad and gain an international competitive edge, TU started to make patent applications abroad for its bainite steel technology. Three of these early applications were made in the USA with the United States Patent and Trademark Office (USPTO) in 1987, 1988, and 1989, one in Australia in 1989, and one in New Zealand in 1989. More recently, TU has continued to make patent applications for related innovations that include technologies from its Mn-series bainite steel development. Examples include patent registrations made with the USPTO in September 2010 and January 2013.
Licensing
The earliest licensing agreement for Mn-series bainite steel came in 1988, when the University exclusively licensed all of its IP for an upfront fee of US $250,000 to Beijing Bainite Steel Co., Ltd. (BBS), which was a joint venture between TU and China Minmetals Corporation (CMC). In 1994, TU desired to increase the commercialization capacity of Mn-series bainite steel. To do so, TU would have to enter into agreements with more than one licensee. The University therefore sold its licenses with BBS so it would be free to find other licensees.
Finding new licensees took some time, but in late 2007 the International Technology Transfer Center (ITTC) of TU found a company (“Company A” for privacy concerns) in the Italian Republic (Italy) that desired to enter into service and licensing contracts with the inventors for the assessment of developing bainite steel for seamless pipes. The result was a services agreement between ITTC and Company A, which was entered into in November 2008.
In 2009, TU’s Mn-bainite steel technology was licensed to a number of companies in the rail, mining, transportation and construction industries in China, Italy and other countries. The licenses have been primarily for using Mn-series bainite steel to develop products such as wear-resistant cast steel, anchor bar steel, high strength and water-resistant steel plates, and high strength finishing rolling rebar.
Commercialization
After Dr. Fang invented Mn-bainite steel, he sought help from the Ministry of Metallurgical Industry (MMI) to promote and commercialize its technology. This early effort in the late 1970s was met with little success as MMI refused his request. Undeterred, the inventor started to promote his technology to companies in the steel and automobile industries through his network of professional contacts and friends. Between 1977 and 1979, a number of steel factories showed interest and collaborated with him on R&D into how the invention could be implemented, but these collaborations achieved few concrete results.
In 1981, Dr. Fang started working with Pangang Group Company Ltd. (Pangang) to produce low carbon granular Mn-series bainite steel. Prototypes were successfully produced and the invention held promise for use in products such as automobile axles, bogies, and connecting rods, but because of the difficulties of mass production, there were limited applications for the technology. A change came about in the early 1990s when the First Automobile Works (later renamed the FAW Group), the Second Automobile Works (later renamed Dongfeng Motor), and Jiangling Motors Co., Ltd., began to use this type of steel in the front axles of their automobiles. With increased interest in Mn-series bainite steel technology from major companies, starting in 1990 the State Science and Technology Commission (the precursor of MOST, the Ministry of Science and Technology) promoted it throughout the country. As a result, the technology became increasingly popular throughout the 1990s.
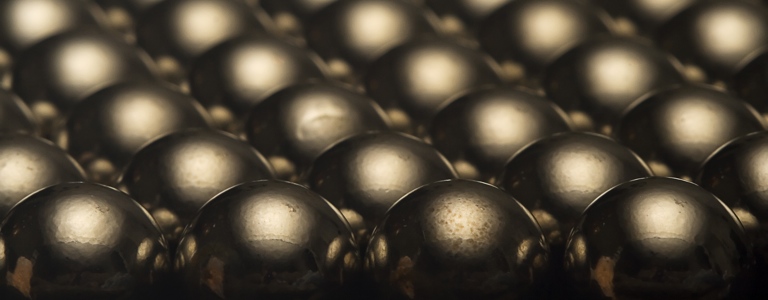
Another important way in which Mn-bainite steel technology was commercialized was through the creation of joint ventures with both large and small companies. The first of these was in 1988, when TU and China Minmetals Corporation (CMC) created BBS. BBS’s most important commercialization success came in 1988, when it cooperated with Tangshan Bainite Steel Group Co., Ltd. (TBS) to establish a township enterprise (market-oriented public enterprises under the purview of local governments). This partnership resulted in using low carbon granular Mn-series bainite steel to manufacture sucker rods for oil fields and steel balls for a variety of applications. Beyond the domestic market, the township enterprise successfully exported its products to Argentina, Australia, Chile, Malaysia, Russia, and South Africa. In 1994, TU sold its interest in the township enterprise in order to regain IP licensing rights. While the township enterprise is no longer the exclusive licensee, as of 2011 it continues to successfully produce and export similar Mn-series bainite steel products.
Although joint ventures played a part in the early successful commercialization of Mn-series bainite steel, the partnership and technology transfer to Jinan in particular brought reverberating positive effects throughout the steel industry in China. The four major companies that licensed Jinan’s JB785 product – Linyi Engineering Machinery Plant (Linyi), Shandong Engineering Machinerey Plant (SEM), Shenyang Air Blower Plant (SAB), and Yantai Penglai Stone-Casting Plant (Yantai Penglai) – have all successfully commercialized a variety of products with promising results.
Linyi uses JB785 to produce parts for the swing arm of loading machines, which reduces the weight by 20% and energy consumption (lighter parts require less energy to move), and also increases operational capability by up to 20%. SEM produces and sells JB785 parts for manufacturing equipment, which are over 20% cheaper and last 185% longer than its traditional equivalent. SAB mainly produces wear-resistant blades for large air blowers, and by using JB785 it reduces manufacturing costs by over 25% and increases product life by over 200%. Yantai Penglai produces JB785 coal transporting pipeline, which is 40% lighter, over 20% cheaper and lasts 243% longer.
IP management
Following the successes of the patenting, licensing and commercialization of Mn-bainite technology, in 2001 the University followed suggestions from the World Intellectual Property Organization (WIPO) and created an official IP management policy. The policy defines IP as patents, trade secrets, know-how, trademarks, copyrights, and any related rights. Under the policy, once a University research project is completed, the researcher(s) must disclose all results to TU’s Achievement and Intellectual Property Administrative Office (AIPAO), which will then determine if any IP rights (IPRs) should be secured. The University strictly prohibits publication and any other disclosure of research prior to any IP applications.
If the technology appears to be commercially viable but not patentable, the University will keep it as a trade secret and take the necessary measures to ensure confidentiality. Any developments that were sponsored by an industry partner (such as a steel company) must be secured by a contract with a clause defining how IP ownership, patent filing costs, and revenue, among others, are shared. This, along with the entire contract with the industry partner, must be examined and approved by AIPAO before it goes into effect. The policy also defines rules related to IP developed by its employees and/or researchers but aimed at domestic and foreign third parties. When this occurs, any resulting IP must be completely or jointly assigned to TU, unless there is an agreement between the researcher(s) and the third party indicating otherwise. Under the IP management policy, at least 40% of all revenue generated from the concerned IP is to be shared with the inventor(s) as cash or equity (such as shares in the company).
The University went to great lengths to ensure that all of its faculty members, students, and staff are properly educated on its IP management policy. As such, everyone working or studying at TU receives a brochure outlining the policy on their first day, and enrollment in an IP education class at Tsinghua Law School is mandatory for all students. In addition, all faculty members in charge of IP management at any University department receive periodic IP training.
With the development of an official IP policy, in the late 1980s and 1990s TU developed a complementary official technology transfer system to facilitate partnerships and commercialization through the creation of five vital entities all working under the National Technology Transfer Center (NTTC) of the University. The first is the previously mentioned RDMD, which has two major functions. First, it manages all commercial contracts related to technology transfer, IP and the dissemination of new technologies. Second, it coordinates cooperation between TU, regional governments and local companies for commercialization. The second entity is the Overseas Research and Development Management Office (ORDMO), which has a mission similar to RDMD, but focuses on organizations, multinational corporations and governments from abroad. The third entity is the University-Industry Cooperation Committee (UICC), which was founded in 1995. UICC’s mandate is to accelerate TU’s technology transfer by strengthening collaborations between the University and various commercial industries. By the end of 2010, UICC has entered into collaboration contracts with 150 domestic and 40 international companies.
Following its creation in 1984, TPA became the fourth official technology transfer entity and was involved in all aspects of patents, from applications to litigation. In 2001, in line with the development of an official TU IP management policy, the agency underwent a structural reform and was divided into the Intellectual Property Management Office (IPO) and the Patent Administration Office (PAO), both of which work under AIPAO. PAO has a broad mandate, which includes the management of all existing patents and future patent applications, invention disclosures, partnerships with IP agencies, and all related fees and funding. In addition, PAO facilitates technology transfer through the assignment of patent rights and patent licensing.
The final entity is the International Technology Transfer Center (ITTC), which was established in 2001. ITTC has become integral to the successful transfer of technologies developed at TU, and works to: help Chinese enterprises find technologies and partners they need in foreign countries; provide services for foreign technologies or products to be introduced or popularized in the Chinese market; provide consulting services for Chinese and foreign small and medium enterprises (SMEs); invest in technologies or products that have been mature in international markets and that have a high potential for success in China; and to conduct academic research concerning technology transfer.
A vital part of the overarching technology transfer system of TU is the Tsinghua Science Park (TSP), which was formed in 2001 and is the only university science park in China. TSP serves as a social outreach vehicle for the University, and it helps incubates start-ups, fosters innovation and promotes the commercialization of TU’s IP. Through promoting the University’s technology and IP, TSP has made significant contributions to the development of the local economy, fostered interest in technology transfer and increased the region’s international competitiveness. These achievements resulted in the establishment of smaller “sub-parks” in the provinces of Jiangzi, Iangsu, Shanxi, Hebei, and Guangdong.
Business results
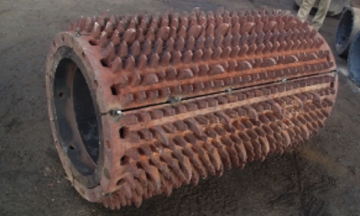
Although Mn-series bainite steel took a rather winding road from R&D to commercialization, the innovative technology has had a fair amount of success. Thanks to a variety of companies working to commercialize Mn-series bainite steel, by 2011 it is used in the automotive, construction and oil industries, in railway transportation, for coal and mining machinery, in high strength seamless steel tubes, in products for ports, and in water and wear-resistant steel products, among others. In the automotive industry alone, for the period from 1997 to 1999, sales of Mn-bainite steel for automobile parts exceeded US $25 million and earned profits of approximately US $3 million. The invention has also been profitable for TU and the researchers involved. From 2009 to early 2011, ten licensing contracts were signed with a total value of US $1 million. Although these agreements have yet to yield royalties as of early 2011, future royalties will be possible through the eventual sale of products by these companies, and TU continues to actively seek new licensees and commercialization opportunities worldwide.
A long yet profitable road
Emerging in a time when technological innovation and IP were still in their infancy in China, the invention of Mn-series bainite steel ignited interest in using technology as a means to grow the economy and become internationally competitive. As IP structures in China matured, the inventors and TU were able to strategically use a strong IP policy, patents and licensing to facilitate commercialization and increase the technological capacity of the domestic steel industry. With increased interest from abroad and the development of a refined type of Mn-series bainite steel in 2009, TU continues to play an important role in economic development and the promotion of technological innovation.
Source: WIPO